How to Use Surface Treatment Technology to Improve the Surface Properties of Glass Bottles?
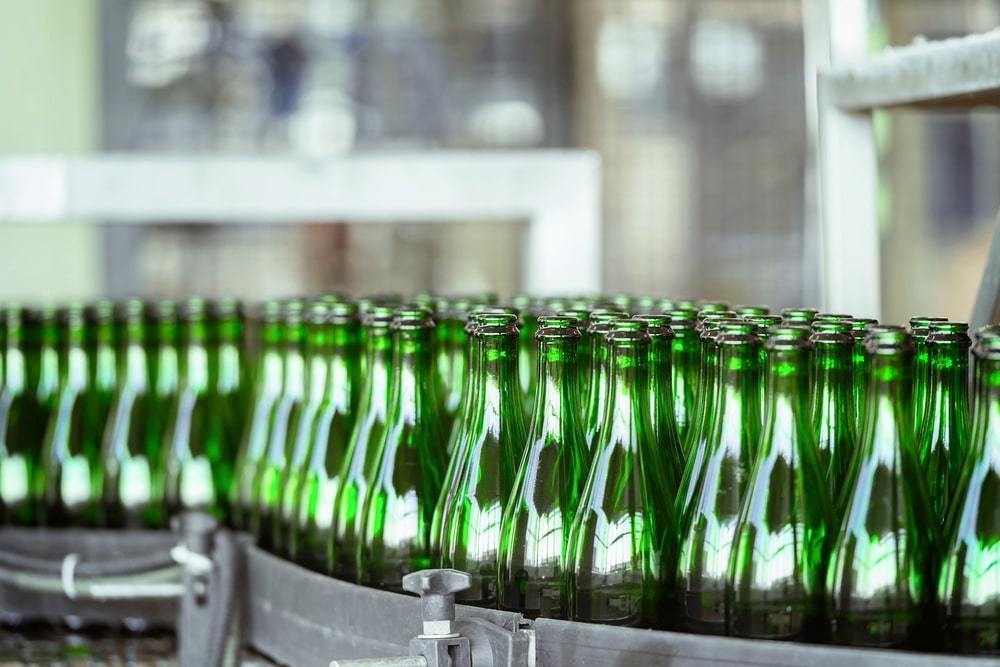
The surface state, composition, and structure of glass are quite different from the internal composition and structure. The surface properties of glass have a significant impact on the properties of its main body. The chemical stability of glass actually depends on the chemical stability of its surface. The mechanical strength and impact resistance of glass are also determined to a large extent by the shape and structure of the glass surface. Therefore, the surface treatment of glass is one of the important technical means for manufacturing high-strength and lightweight glass bottles.
The purpose of glass container surface treatment is to change the chemical stability of the container surface and eliminate damage to the glass surface, so as to achieve the purpose of enhancement. The main methods are as follows:
1. Bottle coating
(1) Hot coating
The hot coating is carried out after the bottle is formed and before the annealing treatment. When the formed glass bottle is slowly cooled to 500-600℃, spray the metal coating agent (such as tin oxide, titanium oxide, tin chloride, etc.) on the surface of the container to form a protective film with a certain thickness to increase the surface strength by approximately 30%, the bottle can withstand long-term water washing and washing.
(2) Cold coating
The cold coating is to spray monostearate, polyethylene, oleic acid, silane, silicone, or other polymer emulsions into a mist after the glass bottle is annealed and adheres to the surface of the glass bottle at a certain temperature. Depending on the spray material, approximately 21~80°C), forming a protective layer with wear resistance and lubricity.
(3) Frosting
The frosting is spraying carbon tetrachloride during the cooling process of the glass bottle or introducing sulfur dioxide in the annealing furnace, both of which can react with alkaline oxides on the surface of the bottle to precipitate sodium ions on the glass surface to form mirabilite particles (I.e. Na2S04 in the form of turbid white powder), after flushing with water, the chemical stability of the surface is enhanced due to the decrease of alkalinity.
(4) Surface organic silicon coating treatment
The use of organic silicon evaporation coating or organic silicon impregnation on the glass surface can form organopolysiloxane hydrophobic film and polymerization (Si02). The silicon-oxygen film is connected to the glass surface through a common silicon-oxygen bond. After heat treatment, the organic groups will volatilize and the remaining silicon oxide film can be filled in the cracks. The hydrophobicity can prevent the diffusion of the active medium in the cracks and cause the surface cracks to heal (commonly known as heterogeneous healing).
This not only greatly improves the strength and chemical stability of the glass, but also gives the glass special optical properties and impact resistance. Commonly used organosilicon solutions include methyl fluoro silane, dimethyldichlorosilane, diphenyl difluoro silane, and phenyl trichlorosilane.
The thickness of the polymer film on the surface of the container is 0.005 mm, and its compressive stress has increased by 10 to 12 Pa under the standard weight of the container. Under the same internal pressure, the weight of almost non-recyclable standard glass bottles can be reduced from 420g to about 300g. The weight of the glass bottle is reduced by 25% to 30%.
At the same time, since the coated film is very thin, the reheating of this glass container will not cause any environmental problems. Therefore, the online polymer-coated container can be included in the standard recycling process.
2. Physical strengthening (tempered)
Physical strengthening (tempering) is also called air-cooling strengthening, the purpose is to improve the mechanical strength and thermal stability of glass bottles.
The physical strengthening treatment method is as follows: After the bottle cans are demolded by the bottle making machine, they are immediately sent into the muffle tempering furnace to be evenly heated to close to the softening temperature of the glass (but cannot reach the softening temperature), and then transferred to the tempering chamber.
Use the air grille of the porous nozzle to spray cold air on the inner and outer walls of the bottle and can to quickly cool the bottle or can, or use the liquid as the cooling medium to suddenly cool the bottle and can, resulting in a compressive stress layer formed by the sudden shrinkage of the product surface. Cooling lags behind the surface as a tensile stress layer. When these two stress distributions are reasonable, the internal pressure strength of the glass can be doubled. The air pressure of the spray bottle body is generally 15-21kPa, and the air pressure of the spray bottle bottom is generally 6-7kPa.
3. Chemical strengthening (tempered)
Ion exchange treatment on the glass surface is also called chemical strengthening. Common methods include a molten salt method and spraying method.
(1) Molten salt method
Exchange the ions with a small radius in the glass with the ion with a large radius in the solute or replace the ion with a large radius in the glass with the ion with a small radius in the solute, so that compressive stress is generated on the surface of the glass, and the internal pressure resistance strength can be improved. High hardness. Wear resistance, the strength of the product will not be reduced due to long-term use.
(2) Spraying method
Spraying chemical tempering has the advantages of good reinforcement effect, safe production and use, high production efficiency, and low production cost. From the perspective of a comprehensive evaluation, it is a relatively ideal reinforcement process at present.
In order to improve the enhancement effect of chemical tempering by spraying method and adapt to the process characteristics, the ideal chemical composition of the basic glass should be selected after research. The chemical composition of the basic glass is different, and the spraying fluid and spraying fluid additive formula should also be adjusted accordingly.
Each process of spraying chemical tempering will have a significant impact on its final enhancement effect. Therefore, two stages of process parameters must be grasped: In the first stage, the formation of the solid phase reagent layer must control the spray temperature, solution concentration, spray time, spray droplet size, solid-phase reagent layer thickness, density, and other parameters; the second stage, heat treatment (ion diffusion and exchange) must control the temperature.
This method can make the strength of the glass container reach about twice the original value, and the loss of the reinforced product during transportation and mechanical filling is reduced to about 1/3 of the original value. The glass product chemically tempered by the spraying method has a good performance gloss and commodity appearance.
4. Surface acid treatment
Surface acid treatment can eliminate a large number of micro-cracks on the glass surface or make the width and depth of micro-cracks smaller, reducing stress concentration. The treatment method is usually to etch the glass product in low-concentration hydrofluoric acid for a certain period of time. In order to make the etching effect better, an appropriate amount of sulfuric acid or phosphoric acid can also be added to the hydrofluoric acid. When the etching depth is 100 μm, the mechanical impact strength of the product can be increased by 50% to 100% and combined with physical toughening, the glass strength can be increased more significantly.
5. Polyester coating
Coat the outer surface of the bottle with a resin (epoxy resin, polyurethane, polyvinyl chloride or polystyrene, etc.) or synthetic rubber coating with a thickness of 0.2~0.3mm using methods such as immersion, casting, and static electricity. The coating can be one or more layers, heat, and harden after coating. This method is simple and inexpensive, but the coating life is short.
If you want to get more information about glass bottle manufacturing after reading the above, DAS Packaging is happy to share some professional suggestions for you.
DAS Packaging, as an experienced glass container manufacturer, our mission is to put the needs of customers first. In order to strictly control the quality of products, we are equipped with a professional production team and a strict quality inspection system. At the same time, we also provide comprehensive customization service. If you are interested in our high-quality glass bottles, please contact us immediately!